Helpful Tools - Enders
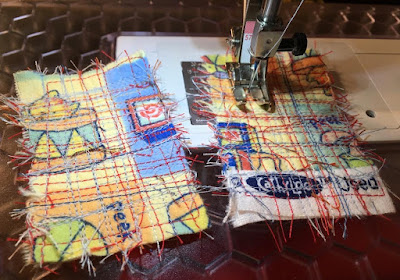
two well used leaders and enders December 2017 Some of the most helpful items I use for sewing are merely scraps of fabric that I use for leaders and enders. Using a leader helps to prevent a needle becoming unthreaded, it also helps to prevent a thread "bird's nest" on the bottom of a project. Personally, I also think it saves thread. I know that some quilters prefer to sew on "Leader and Ender" projects instead of using a scrap like mine. I tried doing that, but got sidetracked and had to finish the project. I tend to switch-out my presser feet often, so using the scrap ender works best for me. This photo shows a ender/leader being used, which allows chain-piecing. More information on these items can be found here and here . If you sew, do you work on a Leader/Ender project or use a single header/ender scrap?